Unveiling the Magic: How Selective Laser Sintering is Revolutionizing Industries!
In the ever-evolving landscape of modern manufacturing, selective laser sintering (SLS) technology stands out as a transformative force. This innovative sls printing service has not only redefined the way products are designed and produced but has also catalyzed significant changes across various industries. With the ability to create complex geometries and customized solutions, SLS is shaping the future of manufacturing. As we delve deeper into the mechanics and applications of SLS technology, we will uncover its far-reaching effects from automotive to healthcare and beyond, setting the stage for a comprehensive exploration of its benefits and potential.
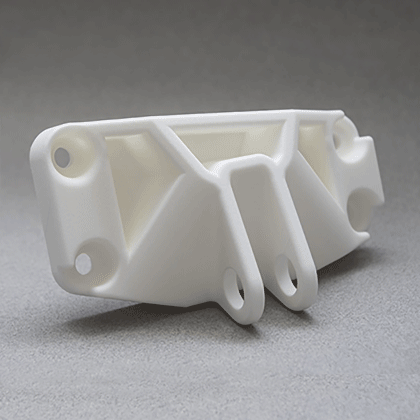
Understanding Selective Laser Sintering (SLS)
At its core, selective laser sintering (SLS) is a 3D printing technology that uses a laser to fuse powdered materials, typically polymers and metals, layer by layer to create solid objects. The process begins with a thin layer of the material being spread across a build platform. A high-powered laser selectively scans the layer, melting and fusing the particles together based on a computer-aided design (CAD) model. Once a layer is completed, the platform lowers slightly, and a new layer of powder is applied. This cycle continues until the entire object is formed. The materials commonly used in SLS include nylon, polystyrene, and various metal alloys, which offer a balance of strength, flexibility, and precision. The mechanics behind SLS technology allow for the creation of intricate details and complex shapes that would be challenging or impossible to achieve with traditional manufacturing methods. Friends who work in engineering often express their amazement at how SLS enables rapid prototyping, allowing them to test designs more efficiently than ever before.
Applications of SLS in Various Industries
The versatility of selective laser sintering has led to its adoption across numerous sectors, each benefiting in unique ways. In the automotive industry, SLS is frequently employed for rapid prototyping, enabling engineers to create and test new designs quickly. This not only accelerates the development process but also facilitates the production of lightweight components that enhance vehicle performance and efficiency. For instance, a friend of mine who is a mechanical engineer recently worked on a project where SLS was used to manufacture prototype parts for electric vehicles, allowing for quick iterations and refinements.
Automotive Industry
Within the automotive sector, SLS technology has proven invaluable for creating functional prototypes, tooling, and even end-use parts. The ability to produce complex geometries means that manufacturers can design components that are both lightweight and strong, contributing to overall vehicle efficiency. Additionally, SLS allows for the rapid production of small batches of specialized parts, which is crucial in the fast-paced automotive market where innovation is key.
Aerospace Sector
In aerospace, the advantages of SLS are particularly pronounced. The industry demands components that meet strict safety and regulatory standards while also being lightweight. SLS enables the fabrication of complex geometries that traditional manufacturing methods cannot achieve, such as lattice structures that reduce weight without compromising strength. This capability not only helps streamline production processes but also enhances fuel efficiency in aircraft designs, making SLS a game-changer for aerospace engineers.
Healthcare Innovations
Healthcare is another field where SLS technology is making significant strides. The ability to create customized implants and prosthetics tailored to individual patients has revolutionized surgical planning and outcomes. SLS allows for the production of patient-specific anatomical models that surgeons can use for pre-operative planning, ensuring better precision during procedures. A friend who is a surgeon shared how SLS-printed models have transformed their approach to complex surgeries, leading to improved patient care and outcomes.
Benefits of SLS Technology
The benefits of selective laser sintering over traditional manufacturing methods are numerous. One of the most significant advantages is design flexibility, as SLS allows for the creation of intricate shapes and internal structures that can optimize performance. Additionally, the layer-by-layer approach minimizes material waste, contributing to more sustainable manufacturing practices. Speed is another critical factor; SLS can significantly reduce production times, especially for complex parts that would otherwise require extensive tooling. These advantages not only enhance overall efficiency but also lead to cost-effectiveness, making SLS an attractive option for businesses looking to innovate and stay competitive in their respective markets.
Transformative Impact of SLS on Industries
Selective laser sintering technology is undoubtedly revolutionizing various industries by providing innovative solutions that enhance design possibilities and manufacturing efficiency. From automotive to aerospace and healthcare, the applications of SLS are diverse and impactful. As we look towards the future, the potential of SLS technology continues to expand, promising even more advancements in manufacturing practices. Embracing this technology can lead to significant improvements in product development, sustainability, and overall industry standards, marking a pivotal shift in how we approach production in the modern age.